Get the Right Product for the Job.
From durable carpet to resilient vinyl, we install commercial flooring products that make the right impression.
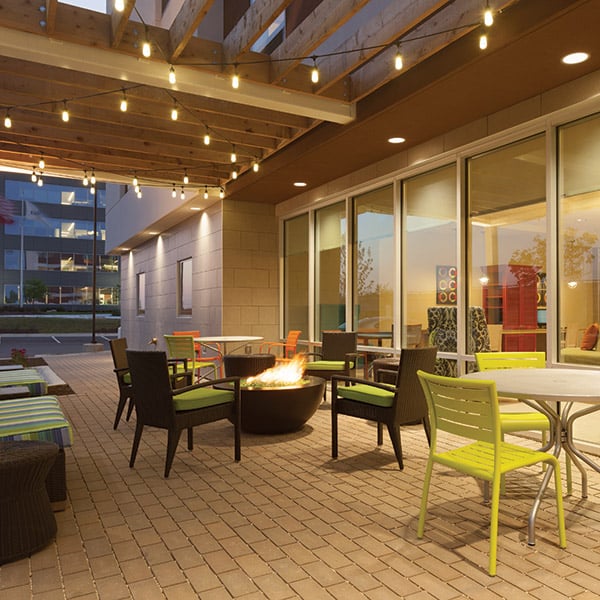
Excelling in Projects from San Antonio to DFW
At Fazio Floors, we understand the value of commercial flooring that balances aesthetics, functionality, and long-lasting quality.
Free from the obligation to any particular manufacturer or brand, our team can order the items specified. If cost reductions are needed, we can value engineer a product match based on quality, performance, and suitability when necessary.
From resilient and easy-to-maintain surfaces to stunning hardwood and eco-friendly alternatives, our commercial flooring products are carefully curated to meet the diverse needs of businesses, offices, retail spaces, and more.
A Few Critical Steps – Skip at Your Own Risk
Surface Preparation
Surface preparation is a critical step in the flooring installation process that involves ensuring the subfloor or existing surface to spec before installing the new floor covering. It involves evaluating and addressing any issues that may affect the performance and longevity of the floor, creating a suitable and stable foundation for the new flooring material.
Here's why surface preparation is essential:
- Subfloor Integrity: Surface preparation allows for examining the subfloor to identify structural concerns, such as unevenness, cracks, or deterioration. Identifying these issues ensures a level and stable surface for the new flooring, preventing future problems and ensuring proper installation.
- Moisture Mitigation: Moisture can pose a significant risk to flooring materials, causing issues such as warping, mold growth, and adhesive failure. Surface preparation involves assessing moisture levels and taking appropriate measures to mitigate any excessive moisture in the subfloor, such as applying moisture barriers or moisture mitigation systems. This step helps protect the new floor covering and ensures its longevity.
- Smooth & Level Surface: Achieving a smooth and level surface is crucial for proper installation and the overall performance of the floor covering. Surface preparation techniques, such as floor leveling, grinding, or patching, are employed to eliminate irregularities, bumps, or depressions, creating a uniform substrate that allows for a seamless and stable installation of the new flooring material.
- Adhesive Bonding: Proper surface preparation promotes optimal adhesive bonding between the subfloor and the new flooring material and ensures a strong and durable connection, preventing issues such as loose or buckling floor coverings. By preparing the surface correctly, the adhesive can bond securely to the subfloor, providing stability and longevity to the floor installation.
- Long-Term Performance: Surface preparation plays a crucial role in the long-term performance of the floor covering. By addressing any existing issues, mitigating moisture risks, and creating a smooth and level surface, the new flooring material can be installed correctly, leading to improved durability, enhanced aesthetics, and reduced maintenance requirements over time.
Moisture Testing & Mitigation
Moisture testing and mitigation of excess moisture are essential steps in the commercial flooring installation process. Moisture testing helps identify potential moisture-related risks before installation, allowing for the implementation of proper mitigation strategies. Before this step can begin, the space needs to be at its operational temperature for at least 48 hours.
Here's why moisture testing and mitigation are essential:
- Protecting Flooring Investment: Excessive moisture in the subfloor can wreak havoc on flooring materials, leading to warping, buckling, adhesive failure, and mold growth. Moisture testing helps identify potential moisture-related risks before installation, allowing for the implementation of proper mitigation strategies. The integrity and longevity of the flooring investment can be protected by addressing moisture concerns before installation.
- Ensuring Proper Adhesion: Moisture can compromise the adhesion between the flooring material and the subfloor. Excess moisture can prevent adhesives from bonding effectively, leading to loose or unstable flooring. Moisture testing enables the determination of appropriate adhesives and installation methods to ensure a strong and durable bond, enhancing the overall performance and longevity of the floor covering.
- Preventing Mold and Mildew: Excessive moisture in the subfloor can create a breeding ground for mold and mildew, posing health risks and causing unpleasant odors. Moisture testing helps identify areas prone to moisture buildup, allowing for targeted mitigation measures to prevent mold and mildew growth, creating a safe and healthy environment for occupants.
- Avoiding Costly Repairs and Replacements: Installing flooring over a moisture-laden subfloor without proper testing and mitigation can result in costly repairs or even complete flooring replacement. Moisture-related issues can cause significant damage and require extensive remediation efforts. Conducting moisture testing and implementing appropriate mitigation strategies can detect and resolve potential problems early, saving time, money, and future headaches.
- Compliance with Warranty Requirements: Many flooring manufacturers have specific moisture-related requirements outlined in their warranties. Failure to adhere to these requirements, such as conducting moisture testing and implementing mitigation measures, can void the warranty. Moisture testing ensures compliance with manufacturer guidelines, allowing for warranty protection and potential reimbursement in case of flooring issues.
Bypass this step at your own risk. We want to help you avoid risks and protect your margins.
Product Acclimation
Acclimation to the building's operational temperature for at least 48 hours (HVAC installed and running) is crucial in preparing commercial carpet, resilient, engineered wood, and hardwood floors for installation, ensuring optimal performance and longevity.
Here's why acclimation is essential:
- Temperature & Humidity Adjustment: Commercial environments often have specific temperature and humidity levels that may differ from the conditions in which the flooring was stored or transported. Acclimation allows the flooring product to adjust and stabilize to the ambient conditions of the installation site, minimizing the risk of expansion, contraction, or other dimensional changes after installation.
- Preventing Buckling & Wrinkling: Flooring not properly acclimated may experience buckling or wrinkling issues post-installation. These issues occur when the floor, still adjusting to the environment, expands or contracts, leading to tension and unevenness. Reduce the risk by acclimating the flooring product to ensure it reaches balance with the installation site.
- Proper Fit & Installation: Acclimated flooring ensures accurate measurements and a proper fit during installation. If floors are installed without acclimation, changes in dimensions due to environmental variations can result in an ill-fitting installation, requiring adjustments or even replacement.
- Minimizing Moisture-Related Issues: Acclimation allows the flooring product to adapt to the moisture conditions of the installation site. The subfloor or ambient air moisture levels can impact the floors' stability and performance. By acclimating, the floor can equilibrate with the environment, reducing the risk of moisture-related problems like mold, mildew, or delamination.
- Proper acclimation is a critical part of the installation process, ensuring that it is ready to perform at its best in the specific conditions of the commercial environment. It helps maintain the floors' appearance, integrity, and functionality, providing a long-lasting and satisfactory flooring solution.
Don’t take chances. Acclimate!